Wire Electrical Discharge Machining (EDM) is a highly precise and efficient manufacturing process that utilizes a thin, electrically charged wire to cut through conductive materials. This technology finds extensive applications in industries such as aerospace, automotive, medical, and electronics, where intricate and complex parts are required. At the heart of this process lie three essential Wire EDM Components that enable the creation of intricate shapes and contours with unparalleled precision. In this article, we will explore these critical components and their roles in driving the success of Wire EDM.
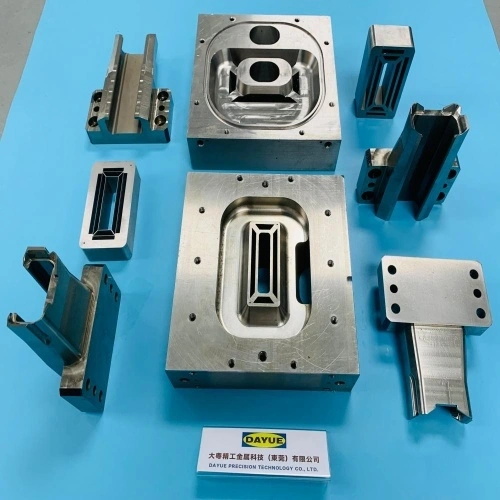
1. Wire Electrode: The fundamental component of Wire EDM is the wire electrode, which serves as the cutting tool during the process. Typically made from brass or coated copper, the wire electrode is a thin, metallic wire with diameters ranging from 0.1 to 0.3 millimeters. Its micro-size enables it to create fine cuts and contours, allowing manufacturers to produce intricate and complex shapes with unparalleled accuracy. During the Wire EDM process, the wire electrode is held between two spools and guided along a predefined path, forming the desired shape in the workpiece. The wire electrode is electrically charged, and when it comes in contact with the workpiece, a series of electrical discharges or sparks occur, eroding the material and forming the required shape. 2. Workpiece: The workpiece is the material to be machined or shaped using the Wire EDM process. It is typically a conductive material such as stainless steel, aluminum, titanium, or exotic alloys. The workpiece can vary in size and complexity, ranging from small intricate components to large molds or dies. The Wire EDM process offers unparalleled precision and repeatability, making it an ideal choice for creating complex and high-precision components. The ability to cut through hardened materials without altering their inherent properties makes Wire EDM an attractive option for manufacturing parts used in critical applications. 3. Dielectric Fluid: The Dielectric Fluid plays a crucial role in the Wire EDM process, serving as both a coolant and an essential element in the electrical discharge process. Dielectric fluids are non-conductive liquids that prevent electrical arcing between the wire electrode and the workpiece, ensuring a stable and controlled cutting process. Dielectric fluid is continuously circulated through the gap between the wire electrode and the workpiece. It not only helps in removing the eroded particles from the cutting area but also dissipates the heat generated during the process, preventing any thermal damage to the workpiece. Additionally, the dielectric fluid provides electrical insulation, ensuring that the electrical discharge occurs precisely at the desired location and adheres to the predetermined path. The use of dielectric fluid also contributes to a clean and smooth surface finish of the machined component.
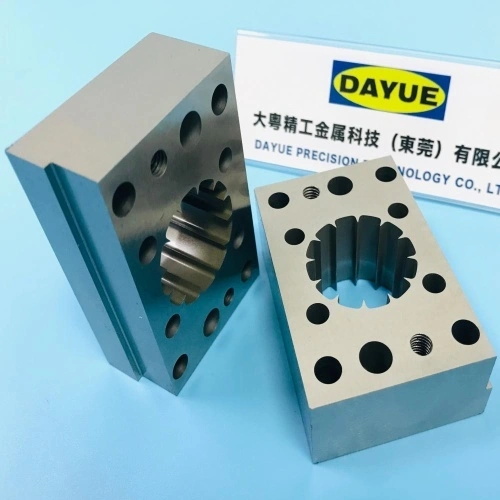
Wire Electrical Discharge Machining (EDM) has revolutionized the manufacturing industry, enabling the creation of intricate and complex components with exceptional precision. The success of the Wire EDM process heavily relies on three key components - the wire electrode, the workpiece, and the dielectric fluid. The wire electrode, with its micro-size and electrically charged properties, forms intricate shapes with high accuracy. The workpiece, typically made of conductive materials, undergoes precise machining to produce intricate and complex components. Finally, the dielectric fluid plays a dual role as a coolant and electrical insulator, ensuring a stable and controlled cutting process. Together, these three essential Wire EDM components form a seamless and efficient manufacturing process, allowing industries to meet the ever-increasing demands for precision engineering and complex geometries. As technology continues to advance, Wire EDM will remain a cornerstone in precision manufacturing, driving innovation across various industries and shaping the future of production. Our company also produces Mold Components and Carbide Tools, if you have any needs, please contact us.